Robert Mann Rugs Opens New Plant in Denver
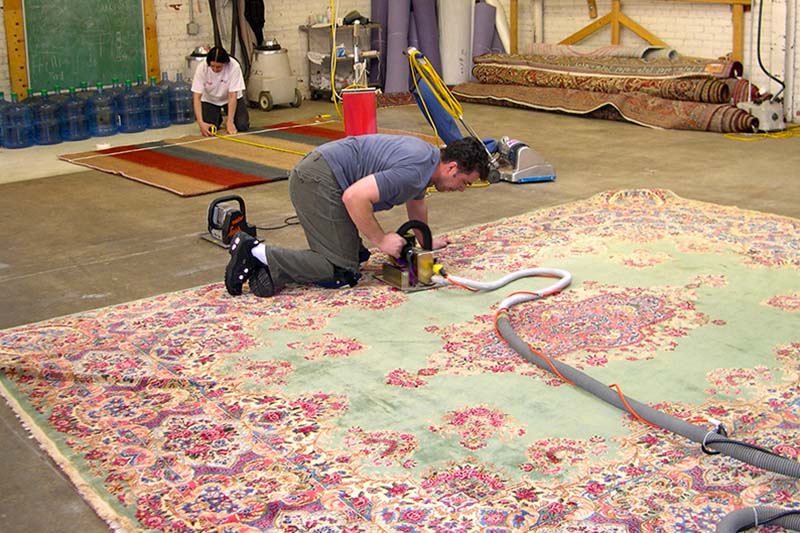
DENVER — June 6, 2019 — Robert Mann Oriental Rugs recently moved into a new, state-of-the-art, 24,000-square-foot rug washing and repair facility in Denver. The previous location was in a 250-acre area of North Denver that was expropriated by the city under eminent domain law. The new plant features a redesigned cleaning and wastewater management system as well as a repair and restoration department.
Master Rug Cleaner Aaron Groseclose recounts the road to the new facility in a letter to the magazine:
Robert Mann is the owner of Robert Mann Oriental Rugs (RMOR) which started in 1978 just doing rug repair, but customer demand for rug washing quickly moved the company to offer this service as well. This most recent move marks the third location in the company’s 41-year history.
The previous Denver location, which housed an excellent repair and washing operation, was expropriated under eminent domain law as part of an area that the city is redeveloping as a new site for the Western Stock Show, Colorado State University, Denver Museum of Nature and Science, and retail shops.
So began a 4-year saga with the city to negotiate the sale of the building, move all equipment, and redesign the wastewater management system to meet current code. Most people would give in to the city and accept a payout, avoiding the hassle of going toe-to-toe, line item by line item with the city attorneys. However, Robert Mann continued to fight the good fight and as a result, he has an incredible facility today — albeit with a few more gray hairs.

Image 1, rug tumblers. Courtesy of Aaron Groseclose.
When a rug arrives at the new RMOR facility for cleaning, its first stop is the tumbler for dry soil removal. This is standard rug cleaning equipment in several countries, but only a few tumblers are found in U.S. rug plants today as they make a comeback after several years of oversight. The tumbler will loosen soil and fibers very effectively and can be used to finish clean rugs. RMOR has tumblers for both dirty and clean rugs (Image 1).
RMOR also outfitted the new facility with a one-of-a-kind Mor® flat-bed compression roller rug washing machine (Image 2). This impressive piece of equipment is 16 feet wide with pressure jets to wash the top and bottom of the rug. The facility also boasts three Cimax® shampoo machines (Image 3). The reasoning to invest such substantial funds in equipment for the new rug plant is efficiency — as volume increases, the current level of employees can remain constant.

Image 2 (left) and image 3 (right) depict rug washing machines. Images courtesy of Aaron Groseclose.
Pressure washing is another important part of the cleaning process. Detergent is applied to the rug on the wash floor, and then the high-pressure washing gun is used for agitation and soil removal (Image 4). The Landa® brand of high-pressure washers are used at 1200 psi. If the rug is extremely soiled, it would be shampooed on the floor (Image 5) before going through the Mor “wash” machine or the “wringer” for additional soil removal, rinsing, and water extraction.

Image 4 (left) and image 5 (right) depict rugs undergoing treatment on the wash floor. Images courtesy of Aaron Groseclose.
To the casual observer it may seem all rugs are cleaned using the same process outlined above; however, each rug is evaluated to determine the best method to remove maximum soil without damage. For example, if the rug has dry rot in the cotton foundation, the tumbler could tear the rug. Certain fibers like viscous could have pile distortion when too aggressive of an agitation device is used (note the second 13-foot-wide Mor machine in Image 4 is without the Cimex machines).
To improve efficiency of the cleaning chemicals, hot water was also added to the system design, delivering warm water continually to the rug at 100 degrees Fahrenheit. The hot water system sends all water through a filter/water softening process (tap water will result in mineral build up), then on to a natural gas direct fire boiler that sits on top of a 900-gallon hot water storage tank (Image 6). The hot water tank holds at 160 degrees Fahrenheit and is connected to two 3500-gallon ‘tempered water’ tanks (Image 7) by way of an elaborate series of valves and pipes that are controlled by a micro-processor panel. The components of this system work together to keep the wash water temperature at about 105 degrees Fahrenheit, continually re-cycling/re-filling the tanks to maintain water supply.

Image 6 (left) and image 7 (right) depict the hot water system. Images courtesy of Aaron Groseclose.
Another challenge was complying with current wastewater management regulations. Denver County tested the rinse water during the design/permitting stages of the project and found it had very low concentrations of soluble waste (chlorine, detergent, acids, etc.) and was virtually a neutral pH. With almost no chemical effluent, the County’s primary concerns became fiber (especially protein fibers) along with sand/grit as these can have a negative impact on the wastewater treatment process.

Image 8, waste collection. Courtesy of Aaron Groseclose.
A system was designed to filter out sand and fiber before the water goes into the sewer, collecting the solid waste in burlap bags and a large tank (Image 8). RMOR pumps out a ’slurry’ of sand and grit once every six weeks or so, which can go into a landfill. All of this came at a very high price tag which was covered by the City of Denver due to the forced move under eminent domain law.
After cleaning, most rugs will go into a centrifuge (Image 9) before drying outside in the Denver mile-high sun (weather permitting) on a 5,000-square-foot concrete slab. Then they go into the dry room onto one of 38 dry poles (Image 10) to finish the drying process.

In image 9 (left), a rug enters the cetrifuge. Image 10 (right) depicts the dry room. Courtesy of Aaron Groseclose.

Image 11 (top), a technician finishes a rug. Image 12 (bottom), RMOR restoration department. Courtesy of Aaron Groseclose.
After drying, the rugs are inspected, pile lifted, spotted, sheared if necessary, and rolled for redelivery to the customer (Image 11).
In addition to rug washing, the new RMOR facility has an excellent repair and restoration department. Collectors and museums from around the country send rugs and other textiles to RMOR for repair (Image 12). They also offer hands-on repair classes to the industry.
The forced move of RMOR was a long and challenging endeavor. Robert Mann has stated, “I am certain I never want to go through something like that ever again,” yet with the mandated reimbursements, tax benefits, and retained assets, the company has benefitted overall and now operates in a fantastic, state-of-the-art facility.
For more on Robert Mann Rugs, check out our Industry Leaders Review of the company in the January/February 2019 issue of Cleanfax.
Aaron Groseclose is the former president of MasterBlend, a manufacturer of rug and carpet cleaning chemicals and equipment. He instructs carpet, upholstery, and oriental rug cleaning seminars. He is the co-developer of the Master Rug Cleaner Program and co-author of A Comprehensive Guide to Oriental and Specialty Rug Cleaning.