A Globally Harmonized System
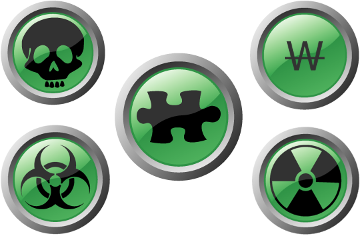
Change is coming to the Material Safety Data Sheets (MSDS) and product labels you have known since your first week in the cleaning industry.
The intent of this change is to have one international standard, which will make it easier to export and import chemical items, as the rules will be the same for all countries who participate.
In the United States, Safety Data Sheets (SDS) become live June 1, 2015 for all manufacturers, and without the new Global Harmonized System (GHS) Safety Data Sheets, no products can be shipped by distributors after December 1, 2015.
Procrastinators were hoping for a two-year delay, which OSHA rejected in November 2014. Canadian adoption of the new rules is proposed 2017 implementation. Official approval in Canada has not been finalized as of the date of this writing.
The primary issue with the June deadline is raw material manufacturers and formulators were given the same deadline. This has compressed the deadline for formulators, as most raw material suppliers have not completed their work, which delays formulators who mix the raw materials into the products you use.
Not only do Safety Data Sheets need to be completed, but Section 2 of the SDS needs to be included on all labels. The label inclusion is a large expense, as new printing plates need to be purchased ($500 each), and old labels will need to be thrown away. There will be many changes on the labels since the warnings required in most cases will take up more space. This will result in less available space for Spanish translation, product descriptions, usage instructions, etc. These will need to be shortened or removed.
As soon as you see the new SDS or labels, it will be immediately obvious that the required warnings are more extensive. Red boxed pictograms will be required to appear on labels and SDS with relevant warnings. (Graphic of these pictograms) The new warnings will make several old familiar products appear much more dangerous than in the past.
For example, our company manufactures a ready-to-use “green” glass cleaner that contain a couple of “green” solvents over one percent. It is much safer than the typical ammonia-based glass cleaner, but the new required warnings give it a dangerous appearance. It uses isopropyl alcohol, the same rubbing alcohol sold to consumers in plastic pint bottles. This rubbing alcohol is about 50 times more concentrated than our glass cleaner. It will be interesting to see the new label for rubbing alcohol, as they will need a label that pulls out like an accordion to accommodate the lengthy list of new warnings.
SDS for ready-to-use solutions
Soon, you will start to see SDS for ready-to-use solutions. Often when a consumer or employee asks for an MSDS for a product, the warnings bring about unnecessary concern. This is especially true with MSDS information for a concentrated product that is diluted before the product even is brought into a consumer’s home or office.
Typically the SDS considers the hazard of each ingredient in the formulation and takes into account the percent of each ingredient. The regulation does not require the reporting of a hazardous ingredient less than 1.0% for most hazards and 0.1% for some hazards. In most ready-to-use cleaning solutions with dilutions over one and up to 32:1 from the concentrate, almost all ingredients will be less than one percent once the product is diluted according to label directions.
Most ingredients are not considered hazardous because they are under the one percent threshold and, therefore, don’t require as many warnings. In short, the Safety Data Sheet for a diluted and ready-to-use products more accurately reflects the appropriate warnings to the consumer and user than the SDS for the concentrate.
OSHA stills requires the availability of MSDS or SDS to be immediately available in the van or anyplace the concentrated product is stored. They reflect the strength of the cleaning solution in the vehicle or workshop. However, if the cleaning solutions are mixed before transporting them to the work site or at the van, then the ready-to-use SDS reflects the accurate warning levels for the product actually used in the home or office.
In Section 12 of the SDS, which is devoted to ecological information, manufacturers and formulators can list the actual percentage of “green” ingredients in the ready-to-use formula, which includes water.
In the end, the transition to Safety Data Sheets will require cleaners to update their MSDS folders with new SDS for all products on their trucks and places of business. Electronic storage can be appropriate in most circumstances.
It is recommended that you have a separate folder for ready-to-use SDS. This format can be used to reassure customers who have some concerns about the safety of the cleaning solutions being used in their homes. This can also reassure cleaners of the risks associated with these ready-to-use solutions with which they clean on a daily basis.
Be sure to ask your supplier for the ready–to-use SDS and use products from those manufacturers and distributors who make them readily available. Your customers will appreciate this more accurate information, and it may save you a lot of grief.
However, there will be some products undiluted products in which the SDS will make the product appear more dangerous than in the past. As with any regulation, there are unclear areas that are open to interpretation.
However, there should be agreement in Section 2 of required warnings for the same raw material. For example, if sodium metasilicate needs to be reported, then the warning for this raw material should be consistent for all manufacturers.
It is our hope that cleaners will be able to make this transition easily. It also is our hope that cleaners understand and appreciate all of the costs and efforts to make this transition by their suppliers.
Tom Forsythe has worked as chemist for Bridgepoint Systems for 15 years and has developed more than 150 products. He has formulated 10 protector products in both the original C8 version and the current C6 versions.